Wind Turbine Gearbox
Wind turbine operator reduced maintenance costs, & improved reliability and equipment life.
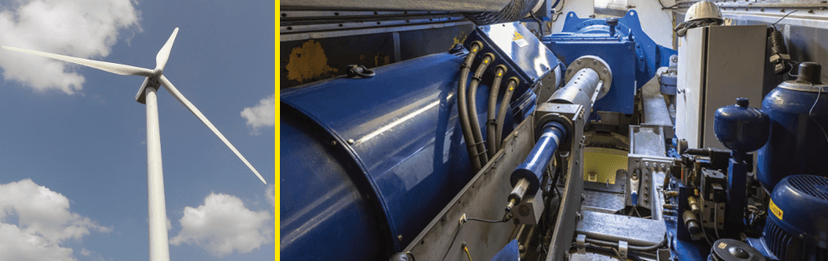
- The customer has reduced daily operating costs, increased power output and extended equipment life.
- - The ability to identify and prevent catastrophic gear box failures, estimated to effect ~ 5% of turbines with a per failure cost of Euro350,000
- - Estimated annual reduction in per turbine maintenance costs of Euro3,500 due to optimised scheduling.
- - 0.5% increase in annual power output over the life of the turbine due to optimal gear box efficiency due to reduced wear.
A large European based operator of wind turbines engaged Tan Delta to integrate full spectrum oil condition monitoring into their existing monitoring and maintenance systems to reduce maintenance costs, extend equipment life and assist with maximizing power generation output.
Over many years of operational experience, the customer had identified the gear-box as the primary source of unscheduled maintenance, sub-optimal power productivity, and long term reliability issues. Extensive trials with Tan Delta confirmed that the accurate real time monitoring of oil condition in the gear box would enable the earliest detection of potential issues such that remedial maintenance could be planned, equipment damage prevented. Analysis of the gear box during the trial confirmed that early detection of issues prevented damage which would cause a reduction in equipment life and power output efficiency. The sensor data was also used to identify and predict the optimal maintenance scheduling.
A single sensor was installed in an oil sample inspection port on the oil return out of the gear box (between the gear box and oil reservoir) where the sensor would be exposed to a continuous flow of oil. Where a turbine had an existing telematics system, the sensor was connected to the modem with the data relayed back to the customers central operations centre. On older turbines where a telematics system was not present a GPRS modem was installed to relay data back to the operations centre. Each installation was completed within 4 hours during normally scheduled maintenance, enabling the entire estate spread across Europe (land and sea based) to be fully equipped within one year.
Each Tan Delta OQSx sensor continuously monitors the real time condition of the oil. Its unique full spectrum hollistic monitoring capability coupled with extreme accuracy, enables any change to be detected and reported in real time - no matter the cause - wear and or contamination. The operations centre used its existing management software to manage and display the data with automatic alerts generated by any unexpected changes in oil condition and using simple trend prediction to pin point optimal maintenance schedules.
After over a year of operation, the customer believes they have seen a significant improvement in maintenance efficiency and their ability to manage each turbine for maximum power output. They also expect that catastrophic failures will be prevented and the operational life extended. Such has been the success of full spectrum hollistic oil condition monitoring the customer is now planning to implement a full roll out.