Concrete
Industrial Condition Monitoring
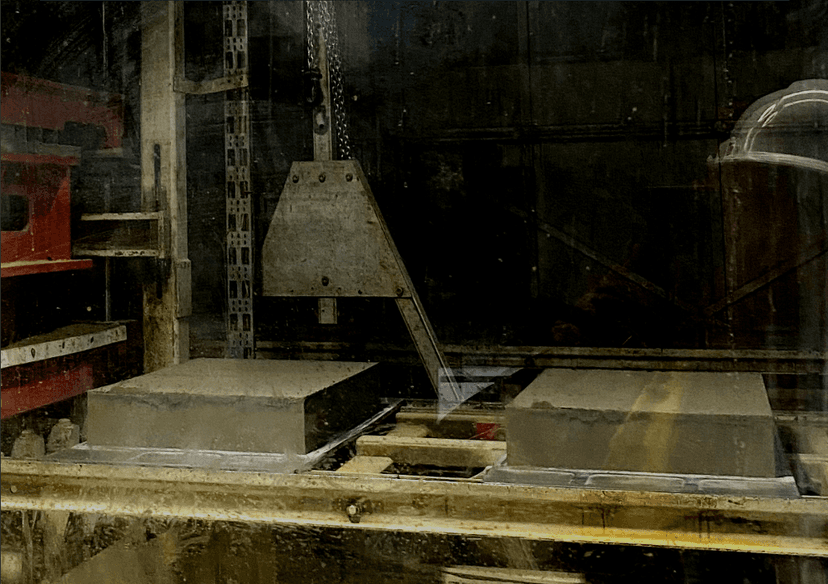
- The continued safe operation of a concrete press operated by a leading UK brick manufacturer is vital to their business. The dangerous environment created by the press means that direct regular access is limited, and requires the machine to be powered down which negatively affects production.
- For this reason, a remote monitoring solution was required to facilitate safe condition monitoring of the hyraulic system as well as fault finding without production downtime.
- Hydrotechnik UK Test Engineering Ltd were tasked with providing a solution.
- A cloud-based solution was decided upon. Using this technology, sensor data can be analysed graphically online from any location.
Cleanliness: The Ptrick Particle counter was placed in parallel with the return line back to tank, to measure the particle contamination in the oil.
Pressure: Three of our HySense PR140 series pressure sensors were installed into valves, and another was inserted into the test point of our flowmeter.
Flow & Temp: Our HySense QT510 flowmeter, along with our HySense TE300 temperature sensor were placed in-line with the main feed from the pump to the manifold.
Watchlog Pro Cloud Monitoring: As the different valves open for different sections of the pressing and stacking cycles, the pressure can be seen on the cloud platform to rise at different times. The sensors were connected to the Watchlog Pro via a junction box with 5m cables. Powered by mains input, the voltage was reduced and transformed to 240VDC to power the system. A single cable then connected the Watchlog Pro unit to the junction unit.